Among the adhesive compositions presented on the construction market, cold welding deserves special attention.
The tool is intended for joining surfaces of various materials.
After using cold welding, two parts form one integral structure.
Cold welding composition
Cold welding is a sheet or in the form of granules material from layers of white and brown. The composition includes epoxy and amine resins, hardener, iron fillers.
For use, a small piece of material for mixing the active substances is separated from the sheet. Only after this the components begin to interact with each other.
Scope of cold welding
• elimination of leaks in pipes, metal tanks, radiators,
• connection of pipeline elements,
• repair of equipment (construction, gardening, household),
• connection of wooden parts, etc.
Material benefits
• provides strong connection of two surfaces,
• resistance to aggressive environments,
• makes it possible to carry out repair work without blocking the water supply, dismantling the structure, in places difficult to access for ordinary welding,
• carrying out welding work near flames and flammable atmospheres,
• pressurize containers not subject to heating,
• used without waste,
• low energy intensity of the process,
• An affordable way to use without the involvement of specialists.
To provide all the nuances of using cold welding, you need to familiarize yourself with the shortcomings of the material:
• pre-heating of the surface of the parts is necessary,
• sometimes a force action needs a shock load,
• some surfaces require processing before polishing,
• size limitation of used parts.
Types of cold welding
Several options are available with identical characteristics and properties.
• by consistency (liquid and plasticine),
• as intended (universal, plumbing, for metal, for use under water, etc.).
Welding should only be used for the surface for which it is intended. The result in violation of the instructions will be either zero or fragile.
The most reliable are high-temperature compositions that have high adhesion.
Instructions for the use of cold welding
1. Before applying the adhesive, surfaces must be prepared. To do this, erase parts of the parts that will subsequently be glued with sandpaper. Then they should be thoroughly treated with an alcohol-containing solution or acetone for degreasing. High-quality preparation guarantees a solid joint surfaces.
2. Separate a small amount of material from a piece of cold welding and knead it with your fingers to give elasticity. The finished product acquires a plasticine structure and a brown tint.
3. To apply the mashed material to the place of connection of parts and secure with a clamp. The pipe can be wrapped tightly in a bundle and left for an hour. During this time, the welding will become hard and can be further processed (drill, thread, etc.). Finally, the adhesive composition hardens in a day.
If you need to perform work on a leaked pipe, and it is not possible to shut off the water supply, then the crumpled material can be pressed against the hole and held tight until it becomes solid. To prevent delamination, tighten the harness around the welding fastener and leave it at least an hour.
The results of surface repair by welding also depend on the conditions in which they are carried out. Humidity does not affect the change in material properties. And the air temperature should not be lower than + 5 °.
It is recommended to store cold welding in temperature conditions from -15 ° to + 35 °. The adhesive composition loses properties at + 150 °. Therefore, for storage, you will need to find a suitable place away from heaters.
Types of joints in cold welding
Welding is carried out using special devices that cause simultaneous directional deformation of previously cleaned surfaces and an increasing stress state in which a monolithic high-strength joint is formed. The quality of the welded joint is determined by the initial physicochemical state of the contact surfaces, pressure (compression force) and the degree of deformation during welding. It also depends on the deformation scheme and the method of applying pressure (static, vibrational). Depending on the scheme of plastic deformation of the workpieces, welding can be spot, suture and butt. Cold welding can connect, for example, aluminum, copper, lead, zinc, nickel, silver, cadmium, iron. The advantage of cold welding is especially great over other welding methods when connecting dissimilar metals that are sensitive to heat or form intermetallic compounds.
Advantages and disadvantages
The advantage of cold welding is that it does not require a powerful source of electricity to heat the welded workpieces. The weld during cold welding of metal is not contaminated with impurities, has high uniformity and high rates of corrosion resistance and stability of electrical resistance. The simplicity of preparing parts for welding and monitoring mode parameters, the absence of auxiliary materials, gas and heat emissions, the ability to remotely control and the speed of the process make cold welding high-tech, do not require highly qualified welder-operator. The disadvantages of cold welding include a relatively small range of materials to be welded (only metals and alloys with high ductility are welded) and significant metal costs by the size of the allowance for butt welding.
Cold welding is widely used in the electrical industry and in transport for connecting aluminum and copper wires, as well as aluminum wires with copper lugs, in electrical installation, in the production of heat exchangers and household appliances. As a type of cold welding, ultrasonic welding is considered - pressure welding with the application of ultrasonic vibrations.
What is cold welding
Under this concept in everyday life, as a rule, we mean a special adhesive composition that is used to connect two different elements into one non-separable assembly. It is this interpretation that will be considered in this article.
Attention! Many people confuse this gluing method with cold welding, which is used in industry. In the manufacturing process, molecules from the contacting surfaces of one substance under high pressure diffuse into another.
Cold welding for metal
This method of gluing metal can be used for both domestic and professional needs, for example, in a car service. For home use, well suited for connecting:
- steel water pipes
- cast iron sewers,
- heating radiators,
- other metal containers (tank, barrel, canister, etc.).
Attention! This type of connection is not a complete replacement for gas or electric welding. It is intended primarily for sealing, and not for being under load during a force action.
The following types of cold welding can be used for gluing metal:
- For metal. They are characterized by high reliability and great durability.
- Universal. Suitable for joining not only metal products, but elements of wood and plastic.
- Automotive. These include special additives that help withstand high mechanical stresses.
- Heat resistant. Parts glued by such welding can withstand heat up to a temperature of 1500 ° C.
- Water resistant. This composition can be used for work under water.
Automotive cold welding is immune to vibrations and large temperature extremes. It is resistant to chemical attack. Such glue is used for repair:
- silencer and exhaust pipe,
- radiator
- gas tank
- bodywork.
On the market, these products are represented by both domestic and foreign manufacturers. The most popular brands for gluing metal:
Cold welding for linoleum
This procedure chemically affects the PVC coating. In fact, the adhesive melts the edges of the two strips of linoleum. Then they are sintered, and at the junction there remains a tight, almost imperceptible seam.
Attention! In such work, care should be taken. Solvents are a part of welding. Therefore, if such an adhesive accidentally enters the coating, aggressive substances may stain it.
This connection method is suitable for any type of linoleum. The method is quite simple and does not require any special equipment. All necessary components are supplied in a cold welded kit. The cost of work is low, it is done quickly. Connecting by this method is not recommended only if the insulation is additionally laid under the coating.
Glue for linoleum consists of two main components:
- solvent,
- filler (liquid PVC).
Depending on the ratio of these two parts in the composition, there are three types of welding for such floor coverings:
- Type A. It contains a large percentage of solvent. Such glue is used when the distance between the two strips of linoleum is less than 1 mm. Due to the liquid consistency, such a solution easily penetrates the gap between the PVC sheets. Be sure to have a nozzle in the form of a needle. This gluing option is considered the most suitable for home use.
- Type C. It contains less solvent. Therefore, such a mixture is thicker. Ideal for joining coatings, the gap between which is from 2 to 4 mm. The tool can be used with and without a nozzle. This option allows you to glue the uneven edges of PVC.
- Type T. Such a composition is rarely used at home. It is mainly used when joining multicomponent materials. The T-shaped nozzle does not allow the surface to quickly absorb the product, as a result of which sintering becomes much better.
The consumption of glue depends on its composition. So, with the more liquid version A, on average, 50-60 ml is spent per 25 meters of the seam. While type C at the same distance you need 1.5 times more.
The main brands of welding for linoleum:
Cold welding for plastic
Bonding plastic parts is another worthwhile application for cold welding. A large abundance of plastic in everyday life makes this type of connection an indispensable assistant for the repair of such products:
- metal-plastic pipelines,
- bumper cars
- fishing rods
- garden tools,
- tourist ammunition
- various plastic products.
Reference! As a rule, not so stringent requirements are applied to plastic welding as to the composition for metal elements. However, here it is also necessary to take into account the further operating conditions of the product: temperature, humidity. And pick up glue depending on the situation.
The composition of cold welding for plastic is more reminiscent of glue for metal than for linoleum. Its composition includes epoxy resin as a base. And the filler is a metal or mineral powder. Due to the absence of heating processes during the connection, the possibility of deformation of parts is excluded. Which is especially important when working with plastic.
To sinter the elements, it is enough to apply glue to one of the surfaces, and press the other to it and fix it with a small press or clamp. When working with plastic pipes, it is necessary to use moisture resistant welding. To fix the elements during the hardening time in this case, a special harness is best suited.
The following products have worked well for bonding plastics:
- Poxipol,
- Mastix,
- Second,
- Super Epoxy Moment,
- Diamond,
- Titanium,
- AVS Crystal.
Cold welding for aluminum (silumin)
Connecting aluminum elements with each other using conventional gas welding is much more difficult than steel. There are two reasons for this:
- low melting point of metal (660 ° C),
- rapid oxidation in the open.
Therefore, for fastening aluminum products, cold welding is often resorted to. It is simpler, cheaper, does not require any professional skills, as when working with argon. Glue is used in various domestic situations and in small industries (car service) for the repair of such products:
- radiators
- boats
- mixers
- tanks, containers,
- window profiles.
The components of welding for silumin are for the most part identical to the adhesive intended for joining the metal. The components are epoxy resin and metal powder. There is a slight difference in the additional additives that can be added specifically for working with aluminum.
Ease of use and low cost not only saves time, but also money. And the exclusion of oxidative processes during the cold welding of silumin gives strength to such a connection.
Attention! It is not recommended to use glue to seal receivers, air collectors and other vessels under high pressure.
When bonding aluminum products, it should be borne in mind that when mixing the components, the hardening process will begin in 20-30 minutes. Therefore, you need to apply glue to the prepared surfaces during this time. Then it is necessary to press the blanks against each other and fix them in this position for about one hour. Final solidification will occur within three hours.
In the Russian market, the following products received the most recognition for aluminum welding:
- WURTH Liquid,
- Titanium,
- Cold Weld Permatex,
- Cosmopur 819,
- Mastix,
- ASTROhimACE-9305,
- Abro Steel.
Cold welding for ceramics
This type of glue is most often universal. Therefore, in addition to faience, it is suitable for working with other materials, such as plastic. However, there are specialized compounds that are used exclusively for ceramics.
This welding is better than others to cope with wet and greasy faces. When working with it, there is no need to thoroughly clean the glued surfaces. It is used to repair such products:
- sinks
- toilet bowls
- ceramic tile,
- other earthenware furniture.
A distinctive feature of this welding is that it leaves an almost imperceptible seam. The period of complete solidification, depending on the brand of glue, can vary from one hour to one day. The main types of welding used to connect ceramic elements to each other:
Cold welding for wood
This type of gluing is used to repair wooden products:
With the help of such welding, it is possible to restore a wooden ornament, eliminate cracks, seal holes from brackets and nails. This is not a very common type of welding, which is associated with the specificity and limited use of this material in everyday life and in production.
The method of application is similar to that used when gluing metal, plastic: prepare the surface, apply, smooth. Drying time is about 30 minutes. The adhesive is moisture resistant and thick enough to prevent spontaneous spreading.
The most suitable compounds for working with wood are:
- Penosil Premium FastFix Wood,
- ABRO AS-224,
- Diamond Tree.
Cold welding for concrete
The product is intended more for fixing some products on concrete than for connecting structures made of it. This is due to the fact that concrete is a fairly hygroscopic material, practically does not absorb moisture. Therefore, in spite of the fact that such cold welding has an increased adhesive ability, it is recommended to use it exclusively for fixing some products on a concrete surface or for connecting small elements together:
- glue fragments of sculptures or monuments,
- fix the mounting boxes and electrical installation,
- close up cable channels,
- repair concrete floors,
- to cover cracks.
The glue begins to harden 20 minutes after its preparation for work. The finally glued product can be subjected to a load not less than one and a half hours after joining.
The main types of glue for concrete:
How to use cold welding
Different types of glue have their own characteristics and characteristics. Some compounds are universal. Others apply to specific materials. Welding may differ in the solidification period and its constituent components. However, there are general rules that allow you to divide the entire workflow into several stages:
- Surface preparation. This step involves cleaning the glued edges from old dirt (paint, rust). To increase the adhesion force, it is recommended to increase the surface roughness by treating it with an abrasive. In most cases, the joints should be degreased with a solvent and only dry materials should be glued.
- Learning the instructions. Before use, it is necessary to familiarize yourself with the main characteristics of the welding used: composition, solidification time, etc.
- Preparation of the mixture. Depending on the type of glue, mix two components into a single substance. The welding components can be in two different tubes or in a common bundle consisting of a core with one material and a sheath with another. It is necessary to mix both components until a plastic homogeneous mass appears.
- Glue application. After the composition is ready, it is applied to abutting surfaces using special nozzles, a spatula or other tool. Then the sintering faces are fixed with clamps, clamps or some kind of press.
- After final hardening, the glued assembly is ready for use or additional processing if necessary.

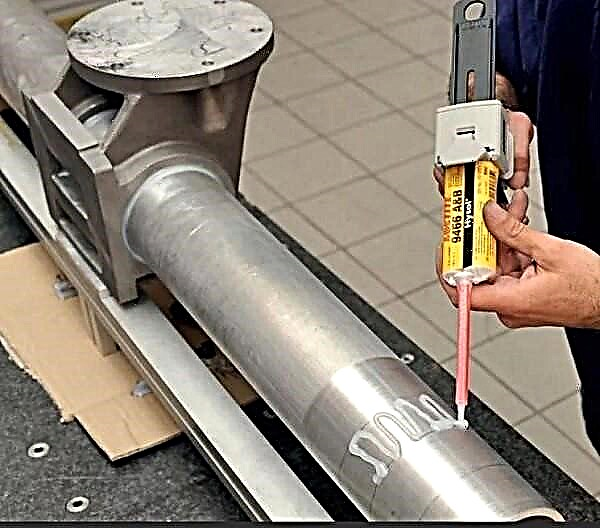
Attention! The full drying time depends on the type of welding and is indicated in the instructions.
Cold welding application
The scope of this type of connection of elements is wide enough. In everyday life and at work, for temporary and permanent repairs, with different types of substances - cold welding is the best solution in all of these situations.
The main materials that can be peeled in this way:
- various metals
- plastic,
- glass and ceramics
- linoleum,
- concrete and stone
- tree.
Special types of welding allow gluing of elements that can maintain their characteristics even with strong heating or when in places with high humidity.
What temperature can cold welding withstand?
Each glue package always indicates the temperature regime at which it can be used. Most brands can withstand heat up to 140 ° C, less often up to 260 ° C. But there are special ones designed for high-temperature operation, when glued parts can be heated to 1500 ° C. Typically, these are used when connecting products made of ferrous metals, which during operation are subject to significant heat.
Does cold welding conduct current
Not a single glue of this type has electrical conductivity. Since the composition of the epoxy resin or liquid PVC, which are dielectrics. Therefore, it does not matter for which material cold welding is chosen (for metal, plastic, etc.) - it will not conduct electricity.
If it is necessary to ensure electrical conductivity, for example, for building bridges on the processor in radio electronics, it is better to use a special conductive glue of the “contactol” type. But it has nothing to do with cold welding.
Cold Welding Composition
Glue is a two-component substance, the elements of which during use react with each other and form the basis for bonding parts. The first component in the form of an epoxy resin or solvent is responsible for the uniformity of mass and ductility. The second in the form of metal powder or liquid PVC is used as a filler. Other substances, such as sulfur and other additives, give the necessary properties for welding, depending on the gluing of which structures it is used.
Benefits of Cold Welding
The use of cold welding makes it possible to connect parts of non-ferrous, noble and ferrous metals, plus to connect dissimilar metals among themselves (copper brazing on aluminum conductors of cables or wires). Basically, this method is used if it becomes necessary to connect metals that can not withstand high temperatures.
The advantages also include:
- Lack of deformation of glued products, because there is no heating.
- The increased reliability of a seam and its accuracy.
- Total lack of waste.
- No energy costs.
- No experience is needed for a cold welding process.
- No tools needed.
- One hundred percent environmental friendliness of the process, without the emission of gases and smoke.
- In some situations, this is the only option (repair of containers in which explosive materials are stored).
Characteristics and composition of cold welding
In fact, this is glue, which includes:
- Epoxy resin, which provides plasticity and uniformity of the weld mass. She is the main one.
- The metal component is the filler.
- Extra ingredients. The list is large, most often manufacturers use sulfur.
The market offers two types: glue cold welding one-component (ready) and two-component.
The quality of the joint is affected by the composition (components) itself, the cleanliness of the surfaces to be welded, and the rules for using cold welding. If all conditions are met, then the weld will be durable. True, it is necessary to indicate that the seam made by any other type of welding is much stronger. Therefore, cold welding can only be used for joining non-load-bearing structures and minor repairs.
The composition of the adhesive component can vary, and it will depend on what temperature the material can withstand. The instructions for use determine this indicator, and if its requirements are observed, then the weld should be strong and will withstand the temperature limit specified in the instructions.
The main types of adhesives for cold welding can withstand temperatures up to + 260C. But there are species on the market that have a temperature limit of + 1316C. They are used in places where conventional types of welding processes cannot be applied.
In its composition, the adhesive used can be:
- Plasticine, this is a bar that needs to be kneaded before use.
- Liquid. This is a two-component option with a hardener added to the base.
Cold Welding Technology
- The preparatory process, which includes cleaning the surfaces of two connected parts. Their degreasing with acetone. It is necessary to achieve that the surface becomes rough, so use coarse-grained sandpaper.
- If liquid glue is used for the connection, then it must be mixed with the hardener. In this case, temperature is usually released. If “plasticine” is used, then before applying it you need to knead it well with your hands.
- In working condition, the glue lasts no more than three minutes, so it must be quickly applied to the welding zone.
- Then two metal products are interconnected. Clamps can be used to create pressure, although this is an optional condition.
How long does cold welding take? It all depends on its composition and manufacturer, but the range is quite wide: from 1 hour to 8.
Attention! Cold welding hardens quickly, so it is recommended to wet your hands with water before use so that the adhesive does not stick to them.
Here is such a simple technology that answers the question of how cold welding works. If you strictly follow the instructions, then the weld should be strong. Do not engage in amateur performances, which will necessarily lead to a violation of the characteristics of the cold compound, for which the instructions are attached.
When it comes to cold welding for cast iron, in most cases the adhesive composition is not used. Here, completely different welding technologies, in which electrodes are used, but the metal is not heated. The technology of cold welding of cast iron is actually very complicated, and its inexperienced welder alone can not be done. The adhesive can be used for minor repairs or temporary solutions to the problem.
Cold welding - recommendations for use
Most often, this type of connection is used for repair work in automobiles. In this way, silencers, radiators, gas tanks are welded. The most important thing is to choose the right composition for the intended purpose. It is understood that parts and assemblies operating under high temperature require the use of heat-resistant material. Do not use universal type adhesive for welding metals. It is better to apply a composition that includes a metal filler.
Never use cold welding for parts that are operated under pressure. This weld has a low tensile strength, the seam will not work under such conditions for a long time. Using the process of cold welding, it is necessary to understand that the higher the temperature the seam can withstand, the higher its strength characteristics.
As you can see, cold welding has excellent properties. And the most important of them is ease of use. Be sure to watch the video - what is cold welding - located on this page of our site.
The advantages of the product include:
- Affordable price.
- No cracks after drying.
- Simple application.
- High reliability after solidification.
- Possibility of application for modeling.
- No shrinkage.
- Resistance to increase in temperature.
We can say that cold welding has no drawbacks, but there are limitations that it has. In that case, if you expect something large-scale from such an adhesive, the modest characteristics of the epoxy composition may seem like a drawback. But still it is impossible to compare this substance with the classical methods of joining blanks. Electric arc welding will always more effectively provide a metal joint, as well as a screw that secures two wooden parts. Glue refers to an emergency method of quick repair or is used in cases where you need to simulate a breakaway part of the product, replacing it with a cured epoxy compound.